Common Construction Scheduling Mistakes
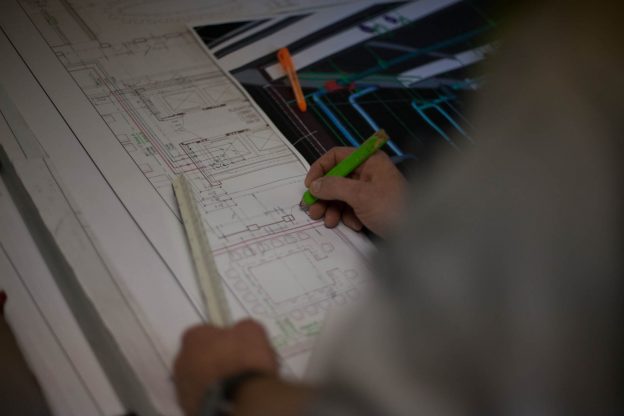
In the construction industry, schedules are extremely important. Being behind schedule on a project can lose you a customer. Creating an accurate construction schedule requires a great deal of thought and attention to detail. Below is a list of some common scheduling mistakes to watch out for.
Common Scheduling Mistakes:
- Failure to consider resources. Contractors and subcontractors all have varying and limited resources. When creating a schedule, it’s important to take a thorough look at what resources you have, what resources you still need, and how long it will take to get those resources.
- Weather. Rain, snow, wind, and severe heat or cold are all factors that will inevitably impact a project at some point. While it’s not possible to predict exactly when inclement weather will strike, or how often, an accurate schedule will assume a certain amount of delay based on weather.
- Unrealistic labor productivity. A good schedule will realistically estimate the efficiency and output of the labor force on the project. With multiple trades working on the same project it’s important to factor in potential delays and the time needed to properly coordinate your trade around the others.
- Lacks detail. For a schedule to be accurate, it needs to be detailed. Different installation methods, materials, etc. can all impact the amount of time it will take to complete a project. A strong schedule will be highly detailed.
- No basis for schedule. Schedules without any basis or proof of why the schedule is set the way it is, will likely not be very accurate or reliable. It’s important to have a solid foundation and logical reasoning to back up your schedule.
For a complete list of scheduling mistakes to avoid, Best Practices Construction Law is a great resource.